Comprehending What is Porosity in Welding: Reasons and Solutions
Comprehending What is Porosity in Welding: Reasons and Solutions
Blog Article
The Scientific Research Behind Porosity: A Comprehensive Guide for Welders and Fabricators
Comprehending the detailed mechanisms behind porosity in welding is crucial for welders and producers striving for flawless workmanship. As metalworkers explore the midsts of this sensation, they discover a globe governed by various variables that affect the development of these minuscule spaces within welds. From the make-up of the base products to the complexities of the welding process itself, a multitude of variables conspire to either exacerbate or minimize the presence of porosity. In this comprehensive overview, we will certainly untangle the scientific research behind porosity, exploring its effects on weld high quality and unveiling progressed strategies for its control. Join us on this journey through the microcosm of welding blemishes, where accuracy meets understanding in the quest of flawless welds.
Understanding Porosity in Welding
FIRST SENTENCE:
Evaluation of porosity in welding reveals vital insights into the honesty and quality of the weld joint. Porosity, identified by the existence of tooth cavities or gaps within the weld steel, is an usual issue in welding processes. These spaces, otherwise effectively dealt with, can jeopardize the architectural stability and mechanical buildings of the weld, leading to prospective failures in the ended up item.
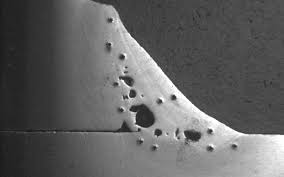
To identify and evaluate porosity, non-destructive testing approaches such as ultrasonic testing or X-ray examination are frequently utilized. These techniques enable the identification of interior problems without compromising the honesty of the weld. By examining the dimension, form, and circulation of porosity within a weld, welders can make educated decisions to improve their welding procedures and accomplish sounder weld joints.
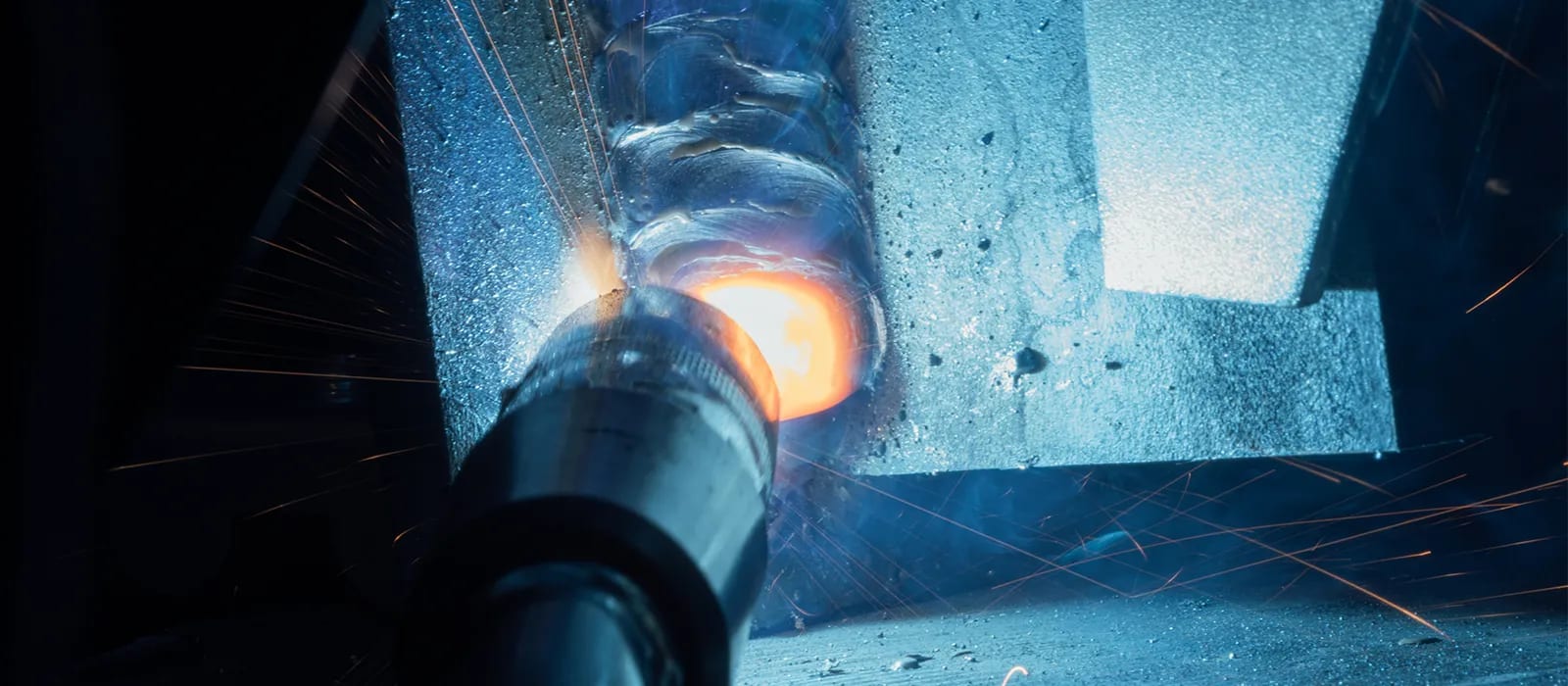
Variables Affecting Porosity Development
The event of porosity in welding is affected by a myriad of aspects, ranging from gas protecting performance to the complexities of welding parameter setups. Welding criteria, including voltage, present, travel rate, and electrode type, also effect porosity development. The welding technique utilized, such as visit our website gas steel arc welding (GMAW) or protected metal arc welding (SMAW), can affect porosity development due to variants in warmth circulation and gas coverage - What is Porosity.
Effects of Porosity on Weld Quality
Porosity development significantly endangers the architectural integrity and mechanical homes of bonded joints. When porosity is present in a weld, it produces voids or cavities within the material, reducing the overall stamina of the joint. These spaces serve as tension focus factors, making the weld extra at risk to fracturing and failing under load. The existence of porosity likewise weakens the weld's resistance to deterioration, as the trapped air or gases within the voids can respond with the surrounding atmosphere, leading to deterioration find out this here over time. Furthermore, porosity can hinder the weld's capacity to endure pressure or effect, more jeopardizing the total quality and integrity of the bonded framework. In important applications such as aerospace, auto, or structural buildings, where safety and sturdiness are vital, the destructive impacts of porosity on weld high quality can have serious repercussions, highlighting the value of reducing porosity through correct welding methods and treatments.
Methods to Minimize Porosity
Furthermore, using the ideal welding parameters, such as the appropriate voltage, existing, and travel rate, is crucial in stopping porosity. Keeping a consistent arc size and angle throughout welding also helps reduce the chance of porosity.

Additionally, choosing the best protecting gas and maintaining correct gas circulation rates are necessary in lessening porosity. Using the ideal welding technique, such as back-stepping i loved this or employing a weaving movement, can also assist distribute warmth equally and lower the possibilities of porosity formation. Last but not least, making certain proper ventilation in the welding environment to remove any potential resources of contamination is crucial for attaining porosity-free welds. By applying these methods, welders can properly lessen porosity and generate premium bonded joints.
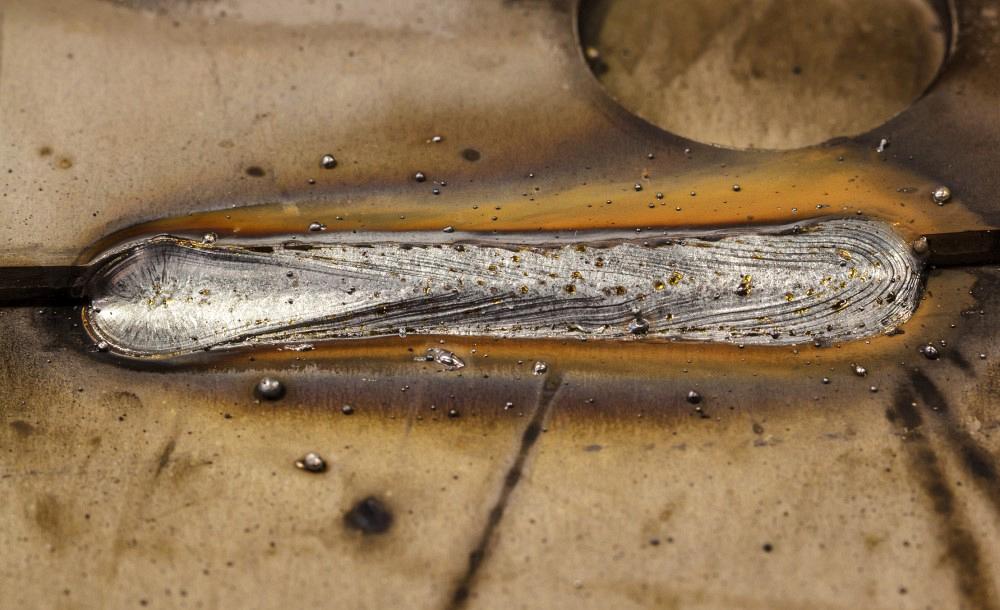
Advanced Solutions for Porosity Control
Executing innovative technologies and ingenious approaches plays a crucial duty in achieving superior control over porosity in welding procedures. One innovative remedy is making use of advanced gas combinations. Shielding gases like helium or a combination of argon and hydrogen can aid minimize porosity by offering better arc stability and improved gas coverage. Additionally, employing sophisticated welding techniques such as pulsed MIG welding or modified environment welding can additionally assist reduce porosity issues.
One more innovative remedy entails the use of advanced welding tools. Using tools with integrated attributes like waveform control and innovative power resources can improve weld top quality and minimize porosity dangers. The implementation of automated welding systems with specific control over parameters can substantially reduce porosity problems.
Furthermore, incorporating sophisticated monitoring and evaluation technologies such as real-time X-ray imaging or automated ultrasonic testing can aid in finding porosity early in the welding process, enabling prompt rehabilitative activities. On the whole, integrating these advanced remedies can substantially enhance porosity control and enhance the total high quality of welded elements.
Final Thought
In verdict, recognizing the scientific research behind porosity in welding is necessary for welders and makers to generate high-grade welds - What is Porosity. Advanced services for porosity control can additionally boost the welding procedure and make certain a solid and reputable weld.
Report this page